Blog: 3D Printed Bar Table and Stools for Formnext 2024
8.1.2025 julkaistuFurniture making and interior design are one of the main uses of robotic fused granulate fabrication (FGF) and it already provides significant design freedom and opportunities for futuristic and innovative designs. However, certain limitations in the process often result in prints being produced in similar ways—most commonly being vase mode printing to create entire finished pieces.
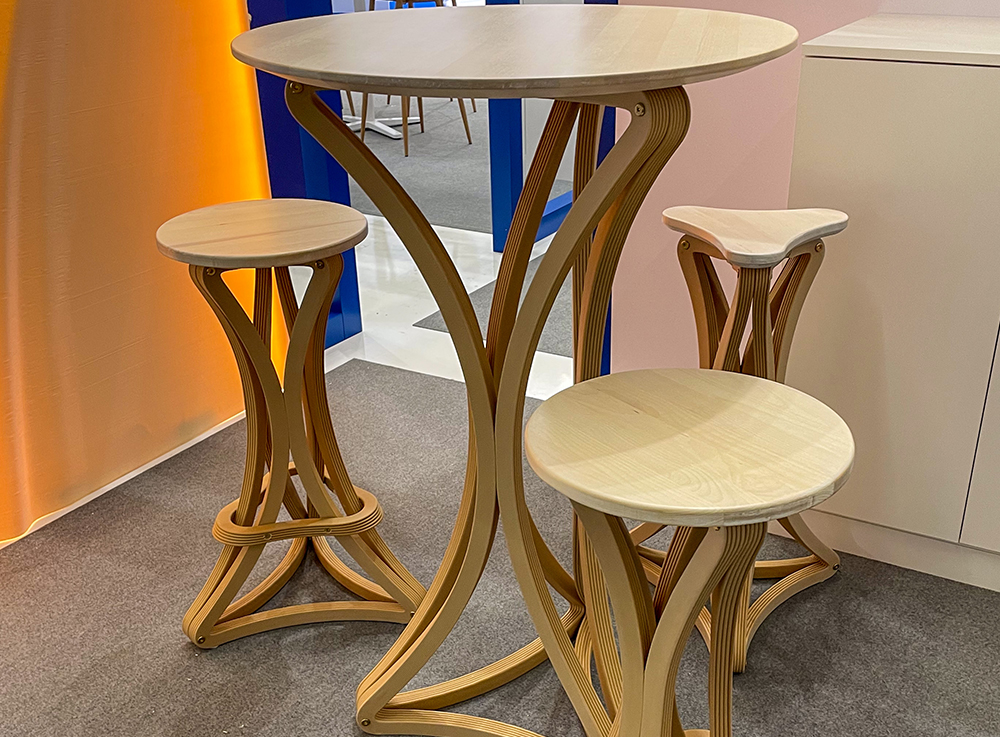
The bar table and stools as presented at Formnext 2024.
This demonstration explores alternative methods to 3D-print furniture by printing separate multiplanar parts on to a curved mold and assembling them into a final piece. In the next section, we take a closer look into the process, exploring its benefits and challenges for advancing 3D-printed furniture.
Coming to the world of large-format additive manufacturing (LFAM), some of the printed furniture pieces appeared notably heavier and bulkier compared to their traditionally manufactured counterparts that serve the same function. One of the reasons for that is the nature of the FGF material deposition process which does not yet in most cases allow for travel moves, relying instead on a continuous extrusion of material.
In simple terms, travel moves refers to the moments when the printer's nozzle moves between points without depositing material. Without the use of travel moves, excess material is sometimes deposited in areas where it is in effect unnecessary, which can add weight and bulk to the final piece. This inefficiency not only influences the production process but also raises questions about sustainability and excessive material use.
Addressing these challenges is essential for raising the quality and variety of 3D-printed furniture and establishing 3D-printing as a practical, sustainable alternative to traditional manufacturing methods.
Design
The most crucial part of the printing process is the initial design phase, where the object takes shape, and the manufacturing workflow is carefully planned. These two elements must work seamlessly together to ensure a successful final outcome.
It is important that designers understand the capabilities and limitations of the technology and apply them to designs in ways that allow for the creation of pieces that are feasible to produce. The pieces were designed by my colleague Maxim Narbrough and evolved into a product through the collaborative efforts of our team.
The geometries were designed entirely using Grasshopper, a visual programming interface integrated into Rhinoceros 3D, a widely used CAD software. Grasshopper was used to develop customized algorithms to shape a printable object, while maintaining full control over key variables, such as bead overlap (how the strands of printed material connect) and the minimum radius of the print path, which are essentials to achieve aesthetically pleasing print.
We also wanted to take advantage of our extruder’s (CEAD E25) ability to print a large volume of material, in this case a bead with a layer height of 5mm and width of 30mm. A bigger bead can be beneficial when printing on a curved surface. Most importantly it requires printing at slower layer times, which also means slower movements of the robot. This helps the robot maintain a more consistent velocity of the axes, especially in sharp turns or other places where the robot orientation needs to change drastically in a short time frame. From previous experiments, we know that unwanted jerking and acceleration of the robot can quickly result in visible marks, surface deformations, or uneven material deposition.
This shows the importance of factoring in bead dimensions when designing for conformal LFAM (3D printing large structures on freeform surfaces), not only for the aesthetics and functionality of the part, but also for the technical manufacturing process.
Manufacturing Workflow
The fabrication process was primarily carried out using CEAD’s AM Flexbot, a robotic-based hybrid manufacturing cell that combines large-format 3D printing and milling into a single turnkey system. First, a minimal mold was printed and milled to its final shape. For the mold, only the necessary surface area was printed to minimize material use and reduce printing and milling times.
To improve adhesion for the next stage, the surface was lightly coated with regular PVA wood glue. Once the mold was prepared, the final part was printed. Subsequently the extruder was again swapped for the milling spindle to drill alignment holes for the furniture screws.
Machining the mold and then printing the part on top using Sulapac Flow 1.7
Challenges
The main challenges in the process were caused by warping, a common issue resulting from material shrinkage as the printed material cools down. In this case, it caused the tips of the printed part to lift off from the mold. Unfortunately, this was the same area where drilling for fixtures needed to be done, which inevitably led to inaccuracies. After a couple of attempts, we were able to predict the effect and adjust the hole positions in the CAD model accordingly to achieve satisfactory results. Warping is difficult to completely eliminate, especially when printing in an open atmosphere without a heated chamber. However, with high-performance, properly dried material, well-tuned print parameters, and carefully designed geometry, the negative effects can be minimized quite well.
Warping causing the print to lift off from the substrate (on a previous iteration of the mold).
However, warping was not the only technical issue we faced. Another common difficulty, especially when printing with larger beads, is material pulling away from outside corners. This issue is somewhat dependent on material properties, but with both materials used—UPM Formi 3D 20/19 and Sulapac Flow 1.7—the results were similar.
This problem was known already before, so we had developed an algorithm, again, using Grasshopper where also the slicing and postprocessing was done, that detects different curvatures of the print path and slows down the feed rate in curves. This gives the soft extruded material more time to cure and stick to its intended position without being pulled away by the moving nozzle. On the other hand, speed is gradually increased in straighter sections to still reach the desired layer time. The function is controlled with a set multiplier which determines how much the speed can alter during the print. Slowing down in turns can also reduce the previously mentioned issue of unwanted jerks and accelerations.
Difference in outside curves caused by the described material pulling. The designed geometry boundaries were machined to visualize the deviation.
Process Times
The printing time for one section of the table leg is 45 minutes, and the drilling operation itself takes less than 5 minutes. However, there are few bottlenecks in the process slowing down the production. One issue is the wait time for the extruder’s top heat zone to cool down below 100 degrees before it can be switched to the milling spindle, which takes about an hour. A potential solution especially in a microfactory setting, could be to implement a cobot (a collaborative robot) or a second robot to perform the drilling.
For the bar chairs, we machined a jig from MDF board using our Biesse 5-axis wood CNC, which was then used for more time-efficient drilling.
Additionally, since the part needs to cool down for at least half an hour before it can be released from the mold and the next one started, a way to streamline the process could be to add one or more additional molds. This would allow for an uninterrupted workflow, notably improving productivity.
A machined drilling jig holds the workpiece with vacuum suction.
Conclusions
To conclude, this demonstration is not only about showcasing the technical capabilities of LSAM but also about exploring additional solutions for small scale mass-production of 3D-printed furniture. Modularity enables efficient packing of the final product, helping to reduce shipping costs. However, it also requires precise and repeatable printing and manufacturing processes to ensure convenient assembly.
The pieces were at display and served as a functional stand furniture for the Finland Pavilion at Formnext 2024, the world’s most important trade fair for the additive manufacturing industry, held in Frankfurt from November 19 to 22, 2024.
Severi Salmirinne,
Specialist in large format additive manufacturing